Design and development of a collaborative human-robot system for asembling, inspection and load/uload tasks in the context of Industry 4.0 using a cyber-physical system with technology based on digital twins
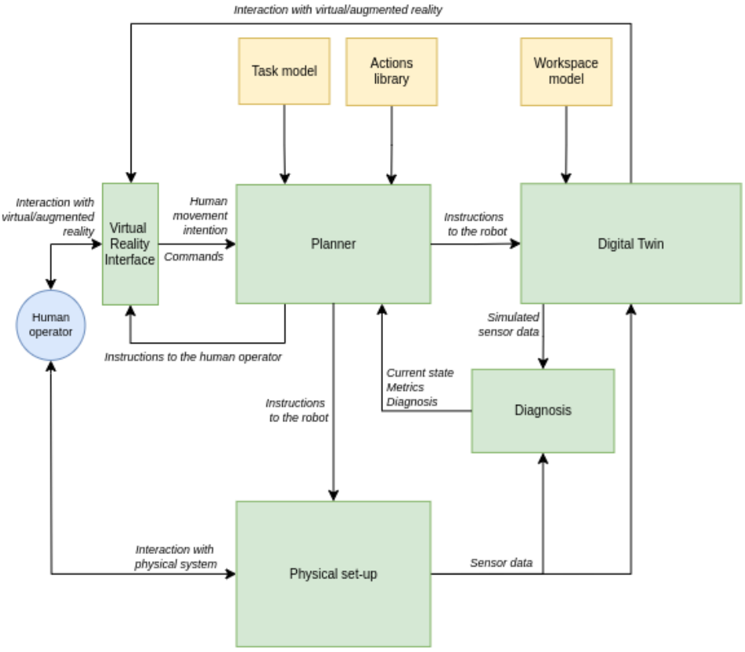
The following specific objectives can be defined:
1. Design and development of a diagnostic system, capable of detecting both failures in the robotic cell elements and in the execution of the collaborative task. It will estimate the current task state and its diagnostique and eventually fault situation. This diagnostic module must learn to incorporate both new types of faults and new information for a better estimation of the current state.
2. Design and development of a dynamic planner, with learning capabilities, that articulates human-real collaboration, both in a real physical environment and in a virtual one based on a digital twin. This planner will provide in each state both the instruction to the human operator and the program for the robotic cell in order to execute the current action of the collaborative task plan. Moreover, it will use the diagnosys information in order to develop a recovery task plan in a fault situation.
3. Integration and evaluation of the efficiency of the proposed system through the execution of a battery of experiments. In this way, a documented study will be carried out to establish how the use of the developed system presents benefits with respect to a conventional collaborative system.